2.加工条件
◆ 加工条件 ◆
・加工レベル:中
電解条件
電極材料名 | ステンレス
|
電極形状 | 2mm diameter
|
電極その他 | ―
|
印加電圧 | ―
|
電流 | ―
|
電流密度 | 0.7A/cm2
|
加工間隙 | ―
|
電解溶液材料 | NaNO3
|
電解溶液濃度 | 20wt%
|
液流量 | ―
|
液温度 | ―
|
pH | ―
|
加工時間 | 120s
|
| 砥粒研磨条件
回転数 | 23rps
|
上下動振幅 | 8mm
|
上下動周期 | 7Hz
|
砥粒材質 | ―
|
砥粒径 | ―
|
砥粒量 | ―
|
研磨材 | ナイロン不織布
|
粒度番号 | 3000
|
研磨材径 | ―
|
|
|
・加工レベル:仕上げ
電解条件
電極材料名 | ステンレス
|
電極形状 | 2mm diameter
|
電極その他 | ―
|
印加電圧 | ―
|
電流 | ―
|
電流密度 | 0.3A/cm2
|
加工間隙 | ―
|
電解溶液材料 | NaNO3
|
電解溶液濃度 | 20wt%
|
液流量 | ―
|
液温度 | ―
|
pH | ―
|
加工時間 | 90s
|
| 砥粒研磨条件
回転数 | 23rps
|
上下動振幅 | 8mm
|
上下動周期 | 7Hz
|
砥粒材質 | ―
|
砥粒径 | ―
|
砥粒量 | ―
|
研磨材 | ナイロン不織布
|
粒度番号 | 3000
|
研磨材径 | ―
|
|
|
◆ 装置図 ◆
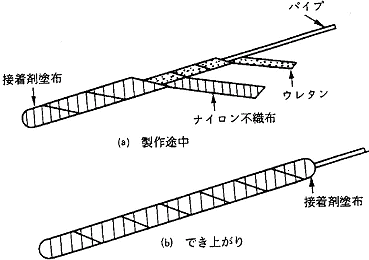
工 具
| 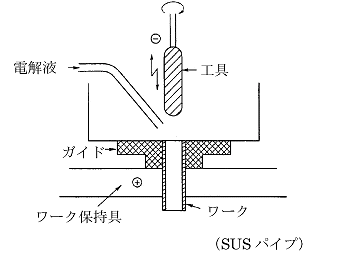
装 置
|